IDLE EQUIPMENT MAY NEED SOME TLC – SO GET A PPM CALL ORGANISED, SAYS WINTERHALTER
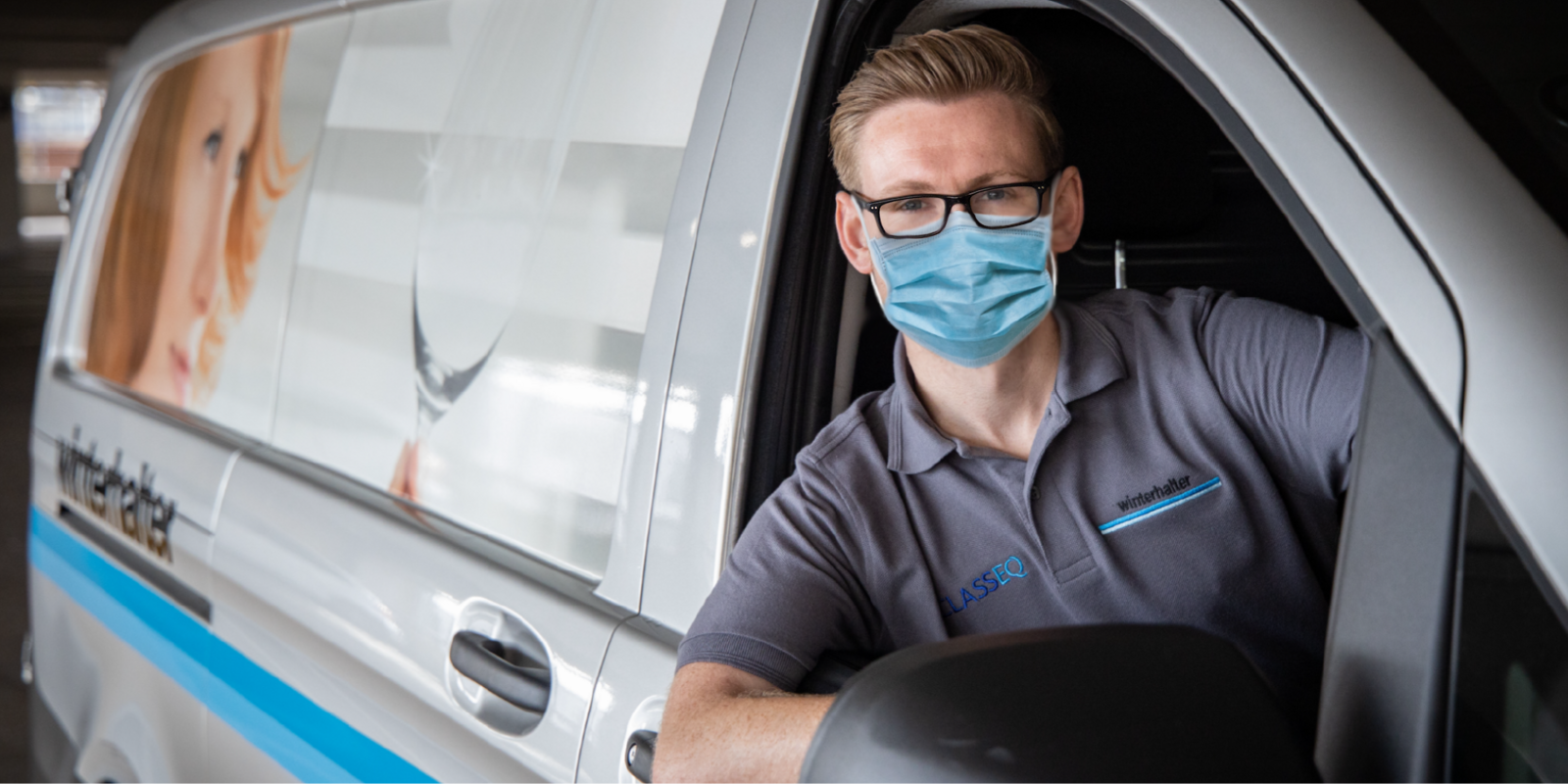
Lockdown offers opportunity to get training on best practice, too
Everyone is looking forward to the end of lockdown. What foodservice operators don’t want is to open up and then have a critical piece of equipment breakdown before they even get going. The problem is, equipment that’s been standing idle may well need some TLC before it’s safe to use. The answer, says warewashing specialist Winterhalter, is to get a planned preventative maintenance (PPM) visit arranged while the kitchen is quiet.
“A reputable service provider will be able to come in at a time to suit the site and will follow the latest Covid compliance regulations in terms of social distancing, PPE and so forth,” says Paul Crowley, marketing development manager at Winterhalter UK. “Our engineers have found that one unexpected plus of a visit during lockdown is that, in a quiet kitchen, there’s more time to discuss areas like best practice and deliver training.”
Another key benefit of arranging a Winterhalter PPM now is that operators who have switched to offer a takeaway service, and find they are washing fewer dishes but more pots and pans, can have the engineer reprogram their dishwasher for use as a utensil washer. “Repurposing the warewasher is a relatively simple process for the engineer, and it’s proving to be very advantageous for quite a few of our restaurant customers,” says Crowley.